By TJ Tedesco
For eighty years, high-volume mail inserting technology didn’t change that much. Until recently, “swing-arm” style mail inserters dominated the U.S. lettershop industry and have done so since the early twentieth century.
Although swing-arm machines still rule the roost in many of today’s lettershops, within the past decade, a new design has gained large inroads. These “continuous-flow” inserters are faster, more flexible, and just as heavy-duty as their predecessors. In short, there’s a revolution going on in the lettershop!
It took some time to get the bugs worked out in the rotary feeder technology used in continuous-flow machines, but they have matured very well. A nice feature of the newer machines is the ability to track production electronically in real time.
Until recently, most high-volume heavy-duty inserting machine manufacturers stuck to their tried and true formula of gathering product and pushing it into envelopes. Although there have been some speed, reliability, and flexibility improvements made over the past half century, they’ve been relatively minor. Swing-arm machines have had basically the same design for a very long time.
A Revolutionary Design
How do the new continuous-flow machines significantly differ from swing-arm inserters?
Consider pocket orientation. When swing-arm machines insert material into #10 envelopes, the inserts travel lengthwise during collation and insertion. On the other hand, continuous-flow machines gather product widthwise, enabling nearly twice as much material to be gathered at the same running speed. Unlike office grade equipment, the envelope-opening device at the end of the production line is similar to that of the more rugged swingarm inserter, allowing it to easily keep pace with pocket feeders during high-speed production.
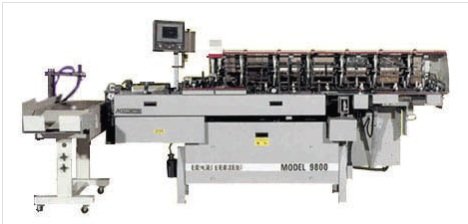
Continuous flow machines cycle 30% to 40% faster than swing-arm inserters and have sophisticated electronic controls that reduce work stoppages by up to 90%. This means that much more mail can be produced in less time with higher yields.
These continuous-flow machines are appropriate for high volume manufacturing environments for three primary reasons. First, many critical parts are manufactured with industrial grade steel instead of lighter-weight materials such as aluminum. Second, like other heavy-duty machines, they are easily adjusted and maintained. Third, the user-friendly, well designed computer interface uses state-of-the-art electronics.
Under the threat of rising postal costs and an advertising world exploding with competing media alternatives, savvy direct mail marketers understand that they need to offer their clients better returns on their marketing investments. Direct marketers must be flexible and able to go from concept to in-home delivery in what seems like a nanosecond.
To learn more about Heeter’s continuous flow equipment, please contact me atttedesco@heeter.com or give me a call at 724-746-8900.
Some of the content for this post was originally published in the newly released Direct Mail Pal 2014, authored by T.J. Tedesco and Charley Howard (publisher: Printing Industries Press).